バックラッシュの改善にはベースの強度が肝になると言うことがわかった。
なので、プラではなく、アルミでいこう。
で、強度があるものは、加工も面倒。
(まあ、3Dプリンターは、そもそも、加工も機械にやってもらうわけだが)
が、私にはCNCフライスがあるからな!!
と、言いたいところなのだけど、加工範囲が狭すぎて、このレベルは無理。
まず、ベースとなるアルミ材。
ジョイフル本田で眺めたところ、300x50x5のフラットバーがあったので、これを使おう。
が、このレベルは切るの大変。
なので、加工サービスで切ってもらいました。楽ちん。
穴開けは、ボール盤で。
で、こんな感じになりました。
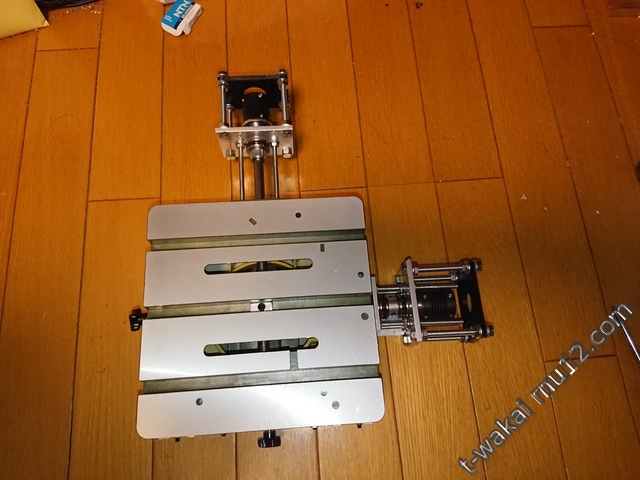
問題となった箇所はこんな感じ。Y軸ですね。
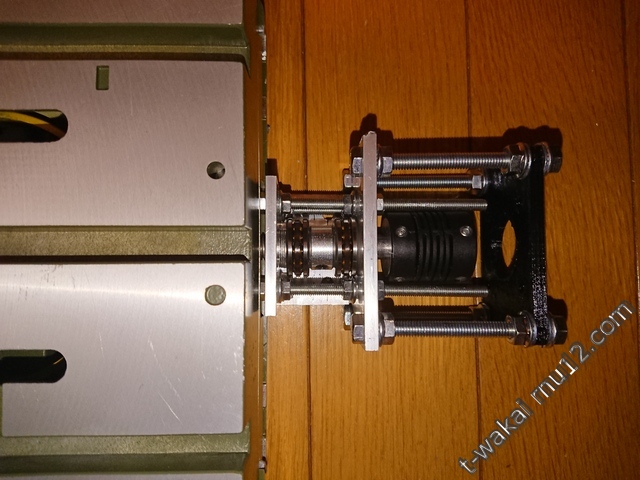
うーん、めかめかしい。
この軸は、中央に回り止めを配置し、左右にスラストベアリングを配置。
さらに外側から、アルミ板で挟み込む。
このやり方だと、ナットを締め付けることで、スラストベアリングにかかる圧を調整できる。
がたのないぎりぎりのところを調整できるね。
ところで、テーブルとベースに全く隙間がないのがわかると思う。
つまり、テーブルは左側には全くストローク出来ない。
半分潰しました。
いいんです。左側にフライスの柱を配置するので、そもそもストロークできないのです。

さて、X軸。
こっちはできるだけストロークを稼ぎたいので、テーブルからベースを離して配置している。
なお、こちらは、軸とベースが一致しているので、本体との取り付けは、ネジだけで十分な強度が確保できる。
軸の保持は、Y軸とは逆で、ベースをスラストベアリングで挟み込み、左右から軸に固定した治具で押さえ込む。
左側はカップリングで押さえ込む形になる。
この方式の場合、微調整が難しい。
うまい具合に押し込んだつもりでも、がたがなくならず、どうしてもバックラッシュが発生してしまう。
(と、言っても0.1mm,0.2mmの話だけど)
なので、対策として、カップリングとベアリングの間にM10のスプリングワッシャーを挟んだ。
これで、軸にテンションがかかるので、がたはなくなる。
この状態で確認すると・・・なくならない。
どうやら、そもそものベースのがたの様子。
まあ、しょうがないね。0.1mmにもならないがたなので。
最後に、ベースへの固定。
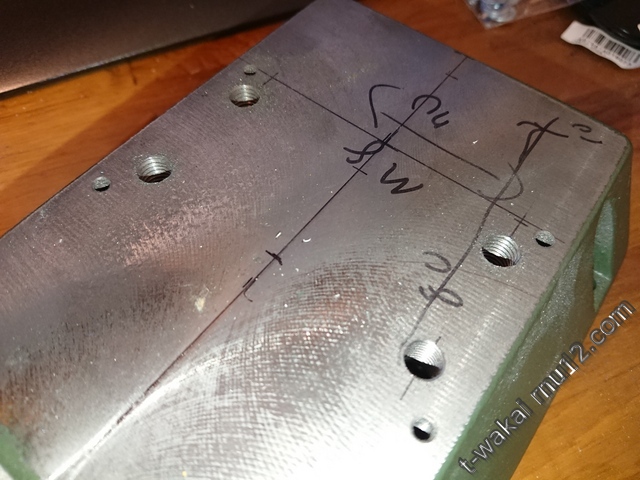
ベースに穴を開け、M8のタップを立てる。
幸い、いい感じの位置関係で固定穴をつけられた。
今回、タップ立てにボール盤を使ってみたけど、いい感じ。
垂直作りやすくていいね。
このあと、組み立てて試運転したが、モーターのトルクがなくてどうにもならない。
大きくなった分、摩擦も大きく、回せない。
調べたところ、ドライバは1.5A程度まで流せるようなので、まだまだいける。
なので、急遽モーターを交換。
秋月に買いに行って、2つ交換。
いい感じかな?
最後に性能確認。
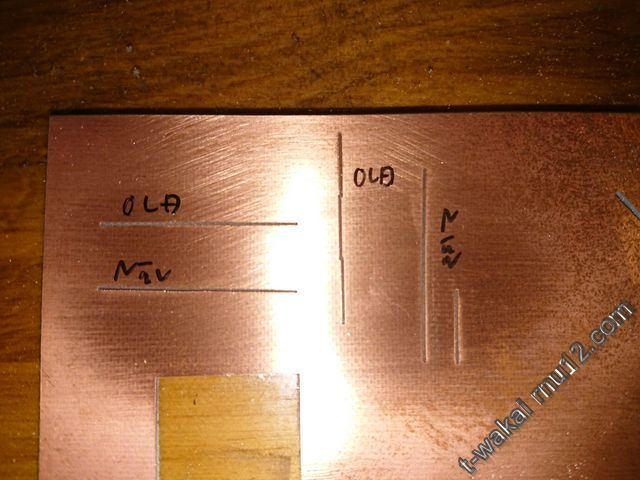
バックラッシュの検証なので、10mmごとに上下左右に動かし、逆方向からアプローチできる感じに。
横方向の切削(Y軸のバックラッシュ)については、新旧大差ない。
よーく見ると、古い方はわずかにバックラッシュが見える。
新しい方は肉眼では確認できない。
縦方向の切削(X軸のバックラッシュ)は古い方が目立つ。
実際、基板切削で配線がなくなってしまった原因。
新しい方は、肉眼では確認できない。
が、旧品でもY軸のバックラッシュは優秀だったことでもわかるとおり、原因はカップリングではない。
動きを見ていると、3Dプリンターで作成したベースが動いているのが見えたので、これが原因だろう。
二重ホースのカップリングの性能は侮れない。と言うか十分かも?
まあ、配線がなくなるほどのバックラッシュはまれだったので、数増やすと問題になるようなケースが出てくるかもな。
なお、採用したカップリング:
アサ電子工業 ADK カップリング EGP28-5-10